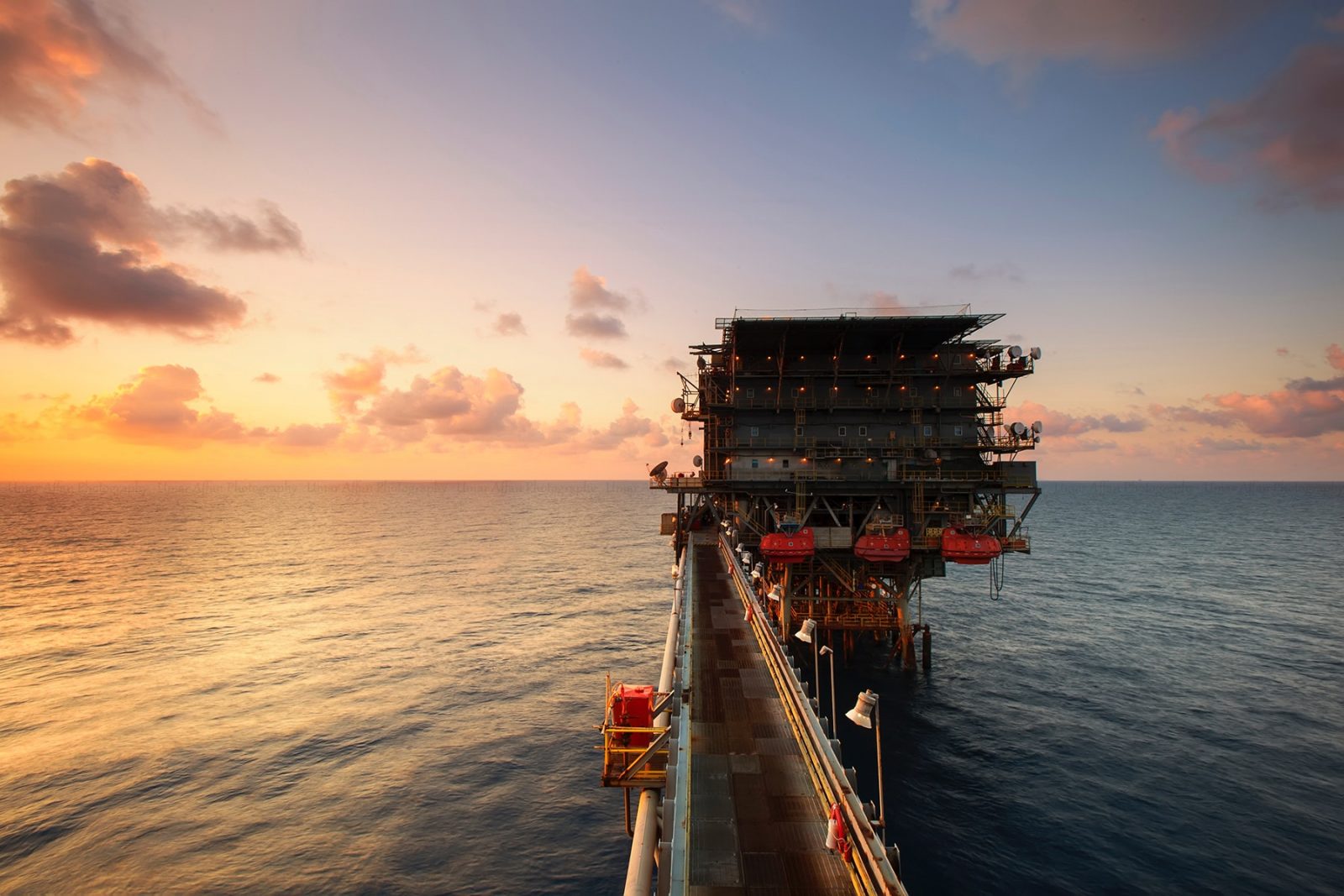
Are you unsure where to start with your work health and safety (WHS) obligations? If so, you’ve come to the perfect place!
In this article, we’ll show you exactly how to measure and evaluate any Work Health and Safety Management system. We’ll walk you through the exact steps you need to take in order to measure the effectiveness of your current work health and safety provisions. We’ll then explain exactly what you need to do to evaluate them and plan your next steps.
Our 3-step Work Health and Safety (WHS) compliance check is suitable for all Australian businesses regardless of their organizational structure, size or industry.
The three steps are:
Step 1: General evaluation
Step 2: Documentation evaluation
Step 3: Worksite evaluation
So if you’re looking to measure evaluate your organisation’s WHS management system, clear your schedule, grab a coffee and let’s get going!
Step 1: General evaluation
The first step of measuring and evaluating your existing WHS management system is conduction a general evaluation. This step will help you get a general feel for your existing WHS provision and give you some indication about the improvements and changes you may like to make in the future.
This initial step is best thought of as a safety self-audit. It won’t give you a full picture of the actual state of your organization’s WHS compliance but it will offer a preliminary indication of where your organization stands. For a complete picture, we recommend you conduct a full WHS compliance audit.
Why take a safety self-audit?
If you’re unsure where to start when it comes to measuring and evaluating a WHS management system, the logical first step is taking a safety self-audit. This gives you a snapshot of where your organization is, where potential weaknesses lie and some suggestions for what you can do to improve your WHS provisions.
How to conduct a general evaluation
If you’re ready to conduct a general evaluation, the first question to ask yourself is, “Do I already have a WHS management system in place?”
Your answer may be ‘Yes’, ‘No’ or ‘Maybe.
If you’re unsure, do you have any system in place that helps you manage your organisation’s WHS compliance? It could be a paper Safety Statement or any type of document that helps you measure risk and safeguard your staff.
The second question to ask yourself is, “What type of system is my organisation using?”
The possible answers you may come up with are ‘Paper-based’, ‘Software-based’ or a ‘Combination/Hybrid solution of both paper-based and software-based solutions’.
If your organization is predominantly working from a safety statement and uses paper forms such as incident reports and risk management forms, then you’re likely using a paper-based system. If you have a mixture of physical forms and electronic files, you’re likely in the third category. If you are entirely software-based, you’ll likely have a dedicated WHS management program in place that helps your organisation manage risks and plan ahead.
That’s it! Step 1 is complete. You should now have some understanding of where your company is at in terms of its WHS management provisions. Let’s move to the second step…
Step 2 – Documentation evaluation
In this second step, you’ll be looking at what documentation your company or organisation has in place. While this won’t give you a full or complete picture like a full WHS management audit would, it will indicate where potential deficiencies are and offer clues about how you can address them.
In this second step of the process, the first question you’ll ask yourself is, ‘Does your company have a signed, up to date Work Health and Safety Management Plan?
The possible answers are ‘Yes’, ‘No’ and ‘Unsure’.
If you’re unsure, consider whether you have an Occupational Health and Safety management plan (OHS) instead. There is some overlap between WHS and OHS plans so it may be that you are covering some of your bases but just labelling the document differently.
The second question to ask in this self-audit is, ‘Does your staff have access to safety documentation at work?’ By safety documentation, we are including policies, procedures, SWMS and other WHS-related documents.
The possible answers to this question include:
- Access to paper copies
- Access to digital copies
- No access, or unsure
It’s common for smaller businesses to give their staff physical paper copies of their WHS documents. This helps them understand how to perform basic duties such as completing a risk management form, filing a safety audit and reporting risks.
Larger companies will commonly share these documents digitally as they are dealing with larger numbers of staff and possibly have their workers split across various physical locations, possibly even across different countries.
If you answered “no access”, or “unsure”, this is one possible area where you may like to make improvements.
The third documentation evaluation question to ask is, ‘How are records of staff, inductions and training managed?’ As with the previous questions, your answers will be limited to paper-based, software-based or having no records. However, you’ll also have the possibility of the records being spreadsheet-based. This is quite common for smaller businesses that take a largely paper-based approach but then record the results electronically on a spreadsheet.
The next question to ask yourself is, ‘How are risk assessments performed?’
The options will be:
- Paper-based
- Spreadsheets
- Software-based
- Not completed
- Unsure
This gives you an understanding of how efficiently your organisation is dealing with risks and how attuned your workers are to noticing and attending to these risks.
To get a sense of how well your organisation’s WHS management system is functioning, you should carefully consider this question: “How are incidents reported to management?” Your options will be either verbally, paper-based (i.e. completing incident reports), spreadsheets (using data from written records), software-based, or (hopefully not) not reported.
The answers to these questions will help you understand where you stand as a company and how effectively you are empowering your employees to report and respond to incidents.
The same goes for the last question in this step: “How are worksite inspections performed and recorded?” The options will be the same as above – either paper-based, spreadsheets, software-based, or not done.
That’s it’s! The second stage is now complete and hopefully, you’re building a clearer picture of how your WHS management system is performing and where potential improvements can be made.
How to analyse your answers
To help you interpret and measure the results you’ve been getting, here’s a brief guide:
If you’ve been answering mostly “Not done” or “unsure”, this indicates that your organization’s WHS management system is deficient in key areas. To ensure legal compliance, you’ll want to investigate ways that you can help your business meet it’s WHS obligations.
If you’ve been answering mostly “Paper-based” or “Spreadsheets” to the above questions, you’ll have to evaluate whether you want to ditch the paper and move towards a more modern software-based approach to WHS management systems. Starting to use a program or WHS app could help your organization improve its current provisions and streamline their processes.
Lastly, if most of your answers have been “Software-based”, you may want to look around at the latest range of WHS management systems offerings. Is there room for improvement? Could you save money and improve your WHS provisions by moving from a software-based approach to a system that uses the cloud? This would help keep your employees aware of their WHS obligations and help everyone stay more connected with the cloud as everything is updated in real-time.
Step 3: Worksite evaluation
We’re finally on to the third and final stage of your WHS management system self-audit. Here, you’re going to be looking at conditions on your worksite and asking whether you can maintain or improve your current situation and if so, with what.
The first question you’ll want to as is, looking around your worksite, “Are each of the following conditions suitable?” The conditions are lighting, noise levels, humidity, temperature, and ventilation. This is a simple check-box assessment – if an area seems suitable, tick it and move on. Any boxes left without a check mark clearly invite further attention. You can ask yourself why these areas aren’t suitable and what can be done to improve them.
The next question to consider is this: “Is there adequate space for members of staff to perform their required tasks?” This is a simple yes or no question. If you’re unsure, ask your staff! A simple questionnaire or informal meeting will give you all the answers you need! If your staff members are generally satisfied with space, move on. If they aren’t, get more details. What’s wrong? How much space do they require? Is it feasible?
Okay – three more questions, but they’re all pretty serious! The next question is about electrical equipment. Ask yourself, “Is all electrical equipment tested and tagged within the required intervals?” This is a simple Yes/No question but the answers are critically important. If yes, that’s all good and well, but if no, why not? This shows a serious lack of attention to detail in your business’ WHS management system – how are such glaring errors going unchecked or unnoticed? This indicates a CLEAR area for improvement!
Next, look at vehicles and machinery on your worksite. (If you don’t have any, move on to the final question) Ask yourself, “How are pre-start checklists/inspections performed?” Is it paper-based, software-based, spreadsheets? Or a hybrid solution?
If they are mostly spreadsheet-based, you’ll want to look at the main ways that you can improve. Would moving to a software-based solution give your staff greater access to data and a higher compliance rate?
Lastly, if hazardous chemicals are used on your worksite, here’s the final question to ask: “Does your chemical register have all of the following in place?”
- Safety Data Sheets (SDSs) that display GHS information
- SDSs that display full business details
- SDSs from the correct companies
- SDSs that are not more than 5 years old
- Registers that include product names, manufacturer and stored quantities.
A cursory glance down this checklist will tell you whether your WHS management system is fit for purpose in terms of storing hazardous chemicals. If there are worrying gaps in your management of chemicals, this indicates that your WHS management system could be improved to help you meet your legal obligations.
How to analyse your answers
Bear in mind that we always recommend that a full WHS compliance audit is carried out to give you a complete picture of your WHS management system. However, this limited self-audit can offer some revealing answers. You can see whether gaps exist in your current provisions and this can help you decide on your next course of action.
If you are answering several of the step-3 questions with “Unsure” or “No” – this shows that a more comprehensive approach to WHS management may be required. If you are completing your requirements but with a paper-based approach, you may like to consider how the latest WHS management software options could help you streamline your business’ WHS requirements and policies.
Lastly, if you are already using a software-based approach, you may like to think about how moving your WHS work to the cloud results in a more streamlined and efficient setup.
Conclusion
WHS management doesn’t need to be complex but hopefully, this brief 3-step process for self-auditing your WHS compliance has given you a preliminary indication of the possible state of your organization’s WHS compliance. While this indication lacks the depth of a full WHS compliance audit (as it doesn’t involve a physical audit) it can help you build a picture of where you’re at, which areas you’re lack and what steps you can take to improve your WHS management provisions today.
If you’re still unsure where to start with your WHS management, give us a call!
Related posts
- Work Health and Safety Management System Software: 10 Key Elements
- WHS Management System: Examples and Key Components